Da dieser Bauabschnitt ein wenig länger dauert und der eine oder andere vielleicht schon mal mit-/nachbauen möchte, habe ich diesen Abschnitt in mehrere Schritte unterteilt. Teil 1 beschäftigt sich mit dem Rohbau des Ständers.
Das Material:
2 x MDF 330x300mm 18mm
1 x MDF 310x250mm 18mm
1 x MDF 310x90mm 18mm
Kosten zusammen ca. 5€
Der Vorteil der MDF (Mitteldichte Faser) liegt in der, wie es die Bezeichnung schon ausdrückt, extremen Dichte der Holzfaser und lässt sich hervorragend bearbeiten. Anders als bei Spanplatten, ist das Holz nicht so spröde. Außerdem lässt es sich -zumindest auf den Flächen- hervorragen lackieren. Im Prinzip ist die Oberflächenbeschaffenheit, der von Metall gleich zu setzten.
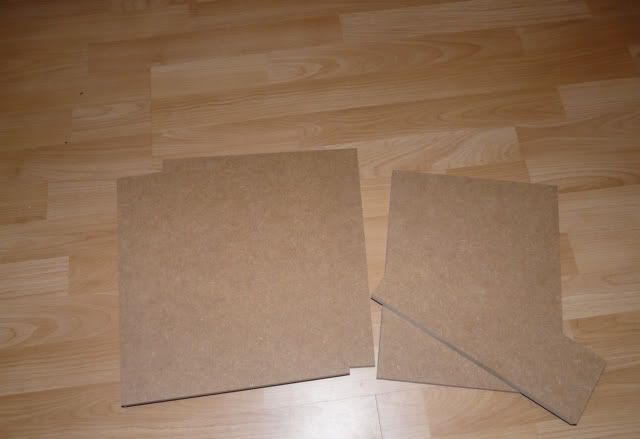
Natürlich darf ein halbes Tom nicht fehlen. In diesm Fall, dass Reststück der Snare weiter Oben, welche aus einem 12x10“ Tom entstanden ist.
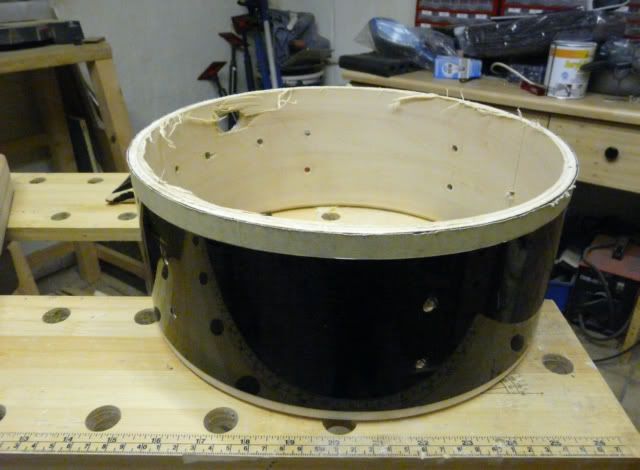
Entlang der 330er Seite, werden Markierungen bei 30 mm und 60 mm gezeichnet. Danach die Markierungen verbinden.
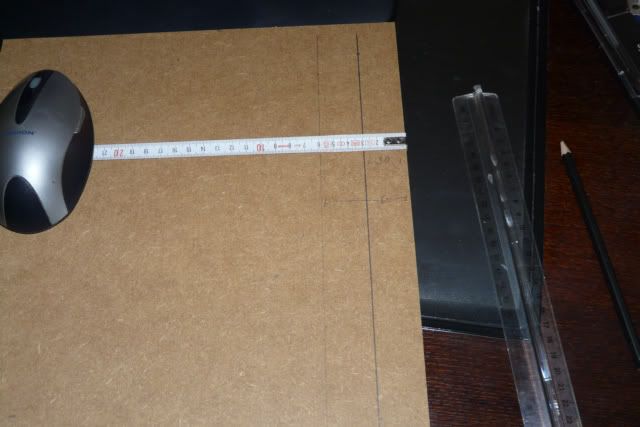
Von oben wird eine Markirung bei 30 mm gezeichnet. An diese Position...
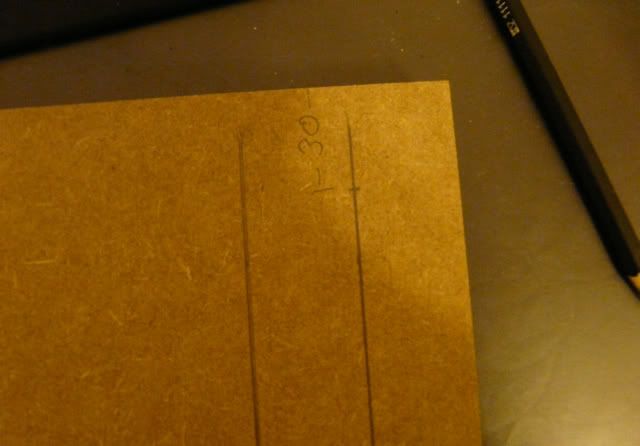
... wird mit einem Zirkel ein Kreis mit einem Durchmesser von 60 mm und 2mm kleiner im Durchmesser nochmals ein Kontrollkreis, gezeichnet.
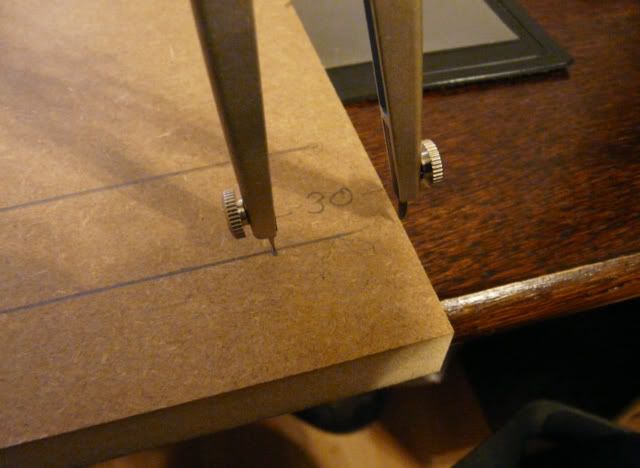
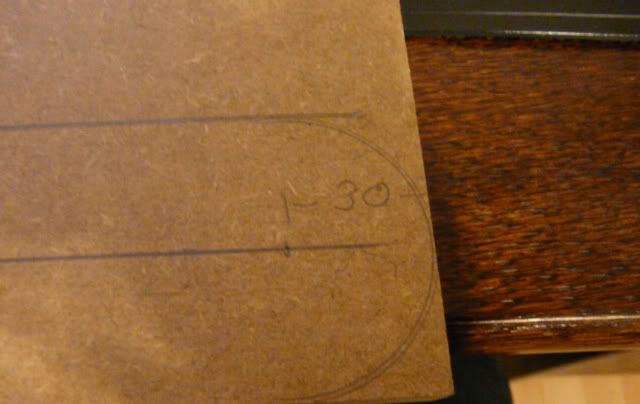
Zur unteren linken Ecke, werden nun zwei Linien parallel zum Kreis hin gezeichnet. Ich habe hier einmal eine Linie im abstand von 50mm und eine im Abstand von 60mm gezeichnet. Durch eine optische Täuschung, wirkt bei einer Schräge der Abstand der Parallellinie größer. Hier entscheidet der Geschmack.
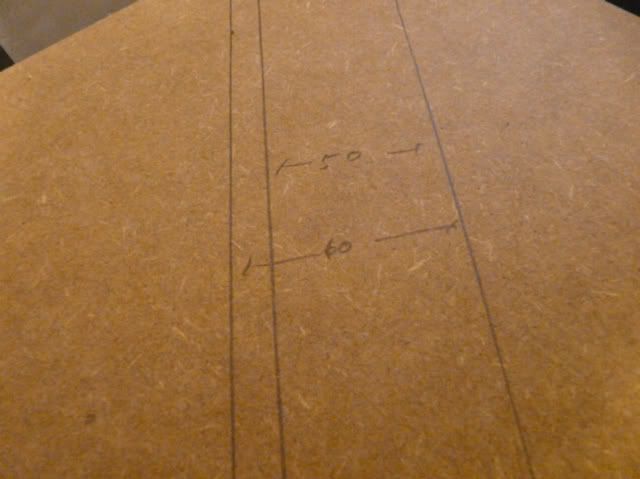
So soll es aussehen
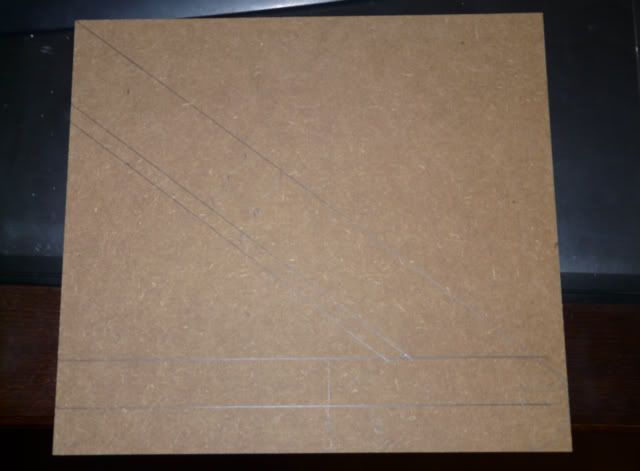
Nun die beiden Platten exakt übereinander legen...
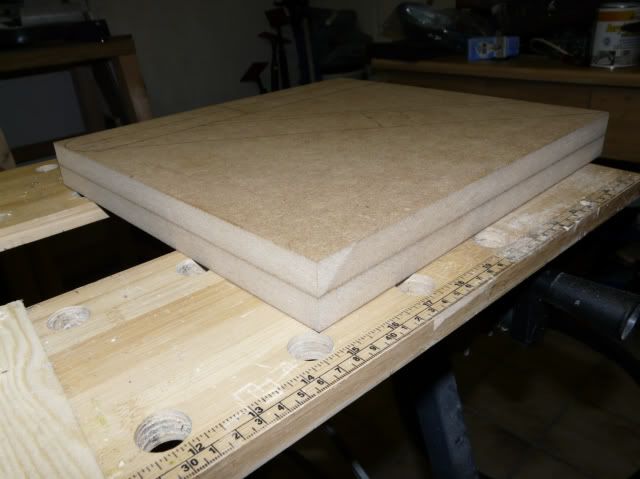
...und möglichst mit Schraubzwingen sichern, damit sie nicht verrutschen. Der Kreismittelpunkt wird nun mit dem bereits bekannten Werkzeug angebohrt.
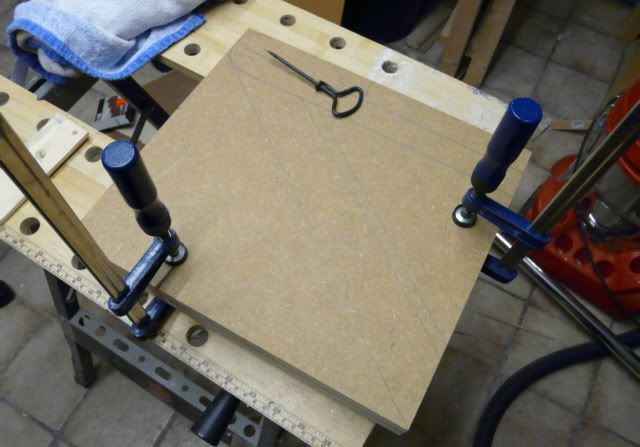
Bitte eine Unterlage zum Bohren benutzen, damit das Holz auf der durchgebohrten Seite nicht ausreißt. Das sieht nicht sonderlich schön aus.
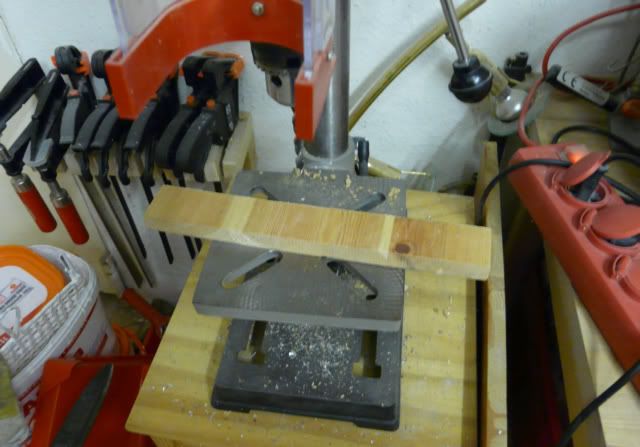
Nun ein 7mm Loch bohren.
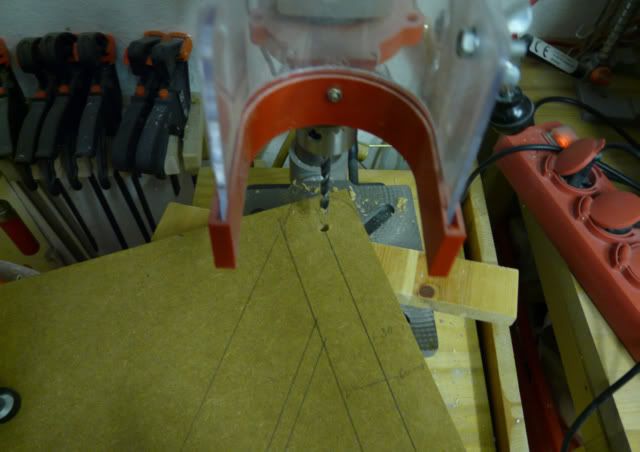
Nach dem Bohren, zunächst den Halbkreis ansägen
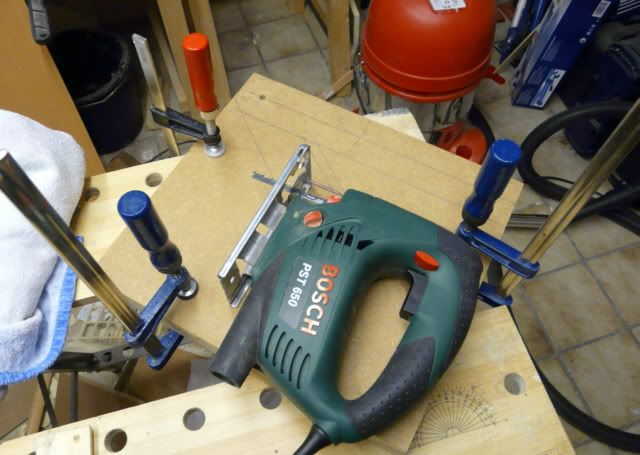
Die beiden Platten nun mit einer M6 Schraube und Karosseriescheiben sichern und mit einer Feile den Halbkreis zurecht feilen
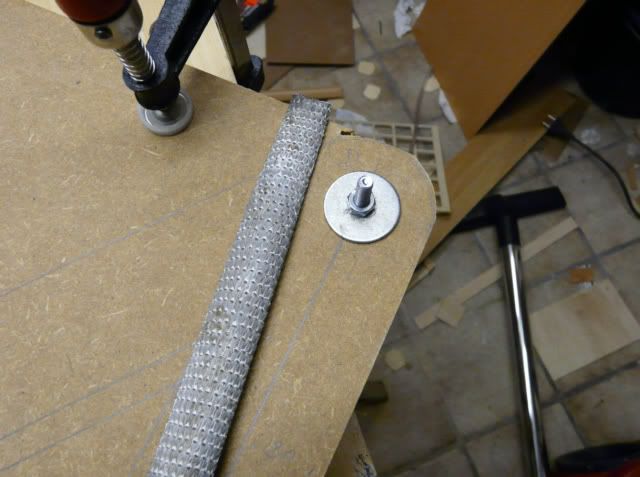
Nun kann entland der Linien gesägt werden.
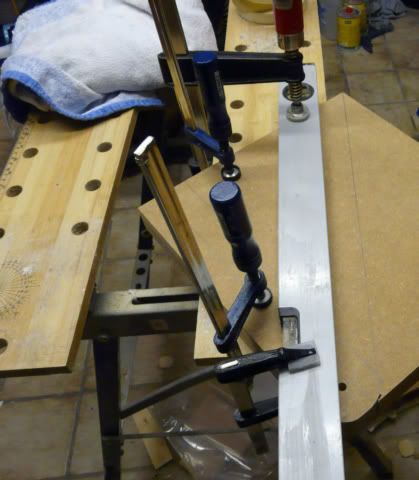
So soll es aussehen
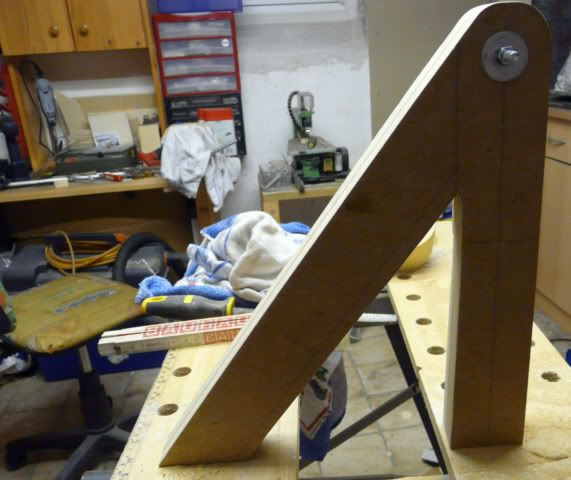
Kaffee trinke, Toilette gehen, weiter geht’s mit dem Kessel. Ich habe den Mittelpunkt zwischen zwei Böckchen gewählt. Die Mitte zwischen den Böckchen anzeichnen und 7mm Löcher bohren. 7Mm deshalb, damit ein wenig Spiel vorhanden ist und die Konstruktion somit nicht zu stramm wird.
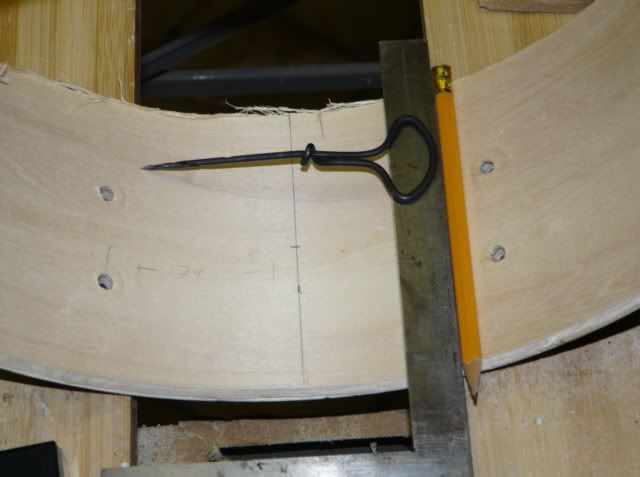
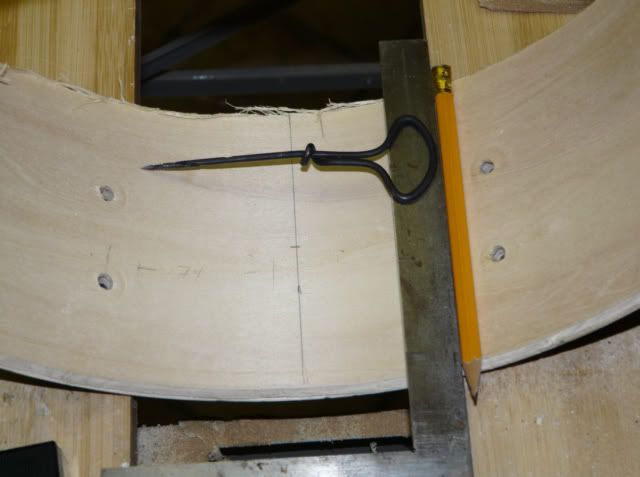
Nun weren zwei Schrauben M6 x 40mm, zwei Unterlegscheiben, zwei Federringe, sowie sechs Karosseriescheiben (im Bild nur vier zu sehen) benötigt.
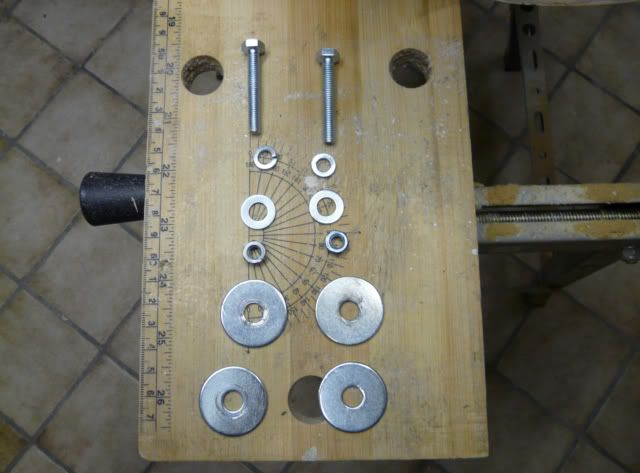
Zur ersten Passprobe, werden die Seitenteile nun an den Kessel geschraubt.
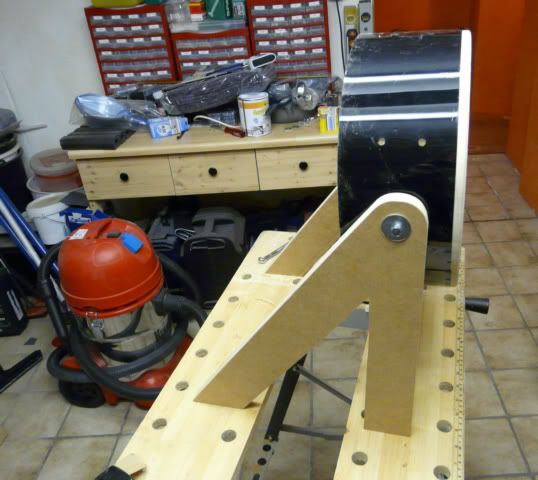
Jetzt geht es an die Rückwand. Hierzu zunächst das 310 x 250mm Brett vor das Tom stellen...
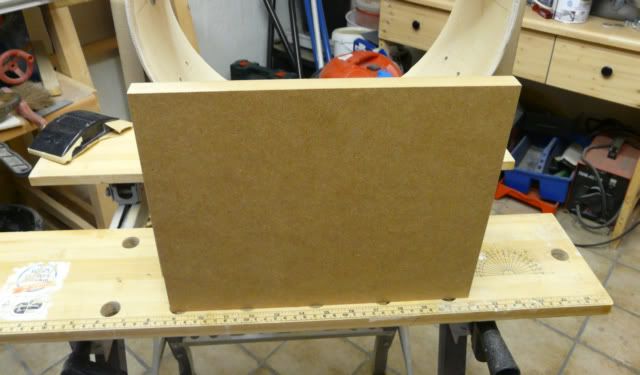
... und genau Links und Rechts ausrichten
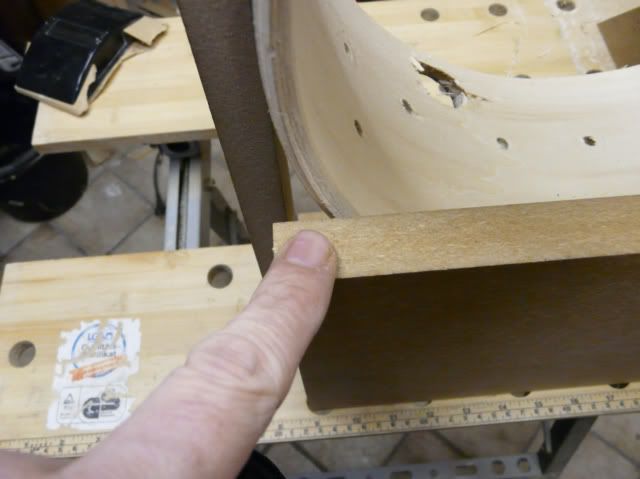
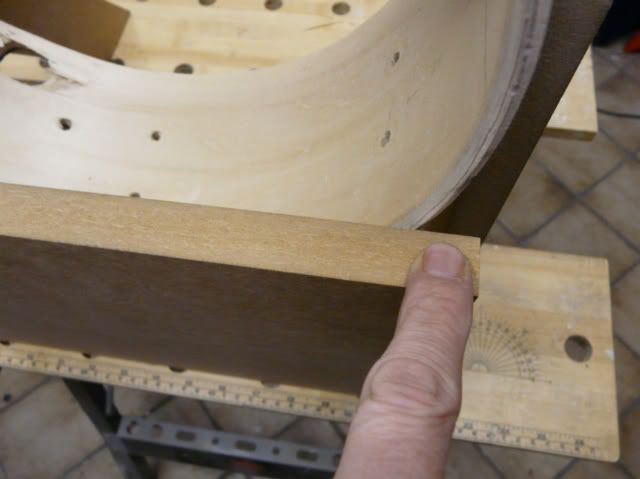
Von der Rückseite nun mit einem Bleistift, an den Rand des Tom entlang den Radius kennzeichnen.
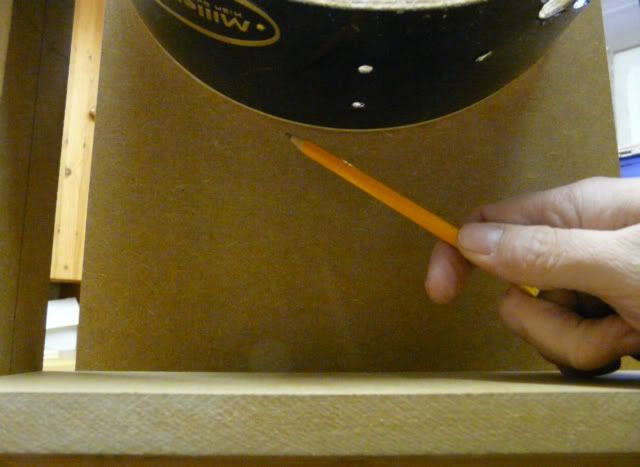
So soll es aussehen
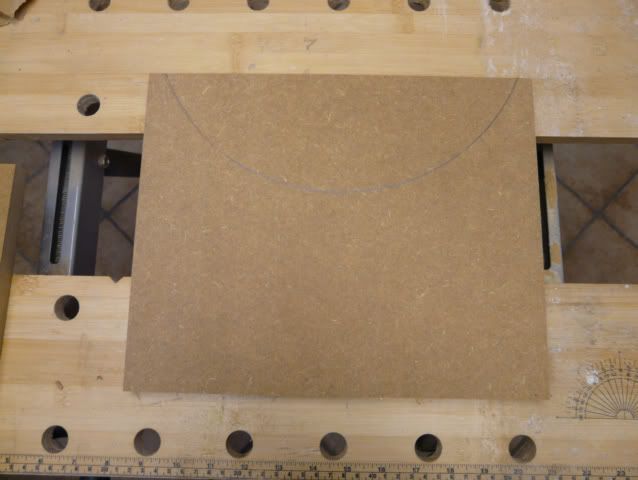
Entlang der Kennzeichnung mit einer Stichsäge aussägen
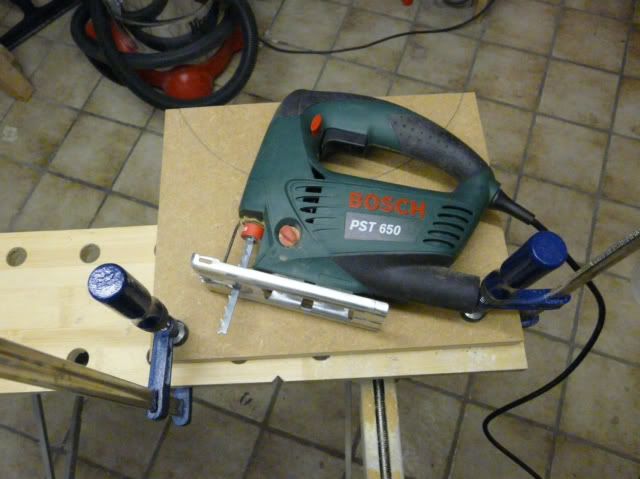
Da es selten gelingt, freihändig mit einer Stichsäge genau zu sägen, sind nun Anpassungen notwendig. Hierzu das Brett vor das Tom stellen und so lange mit einer Feile bearbeiten, bis das Brett genau unter das Tom passt.
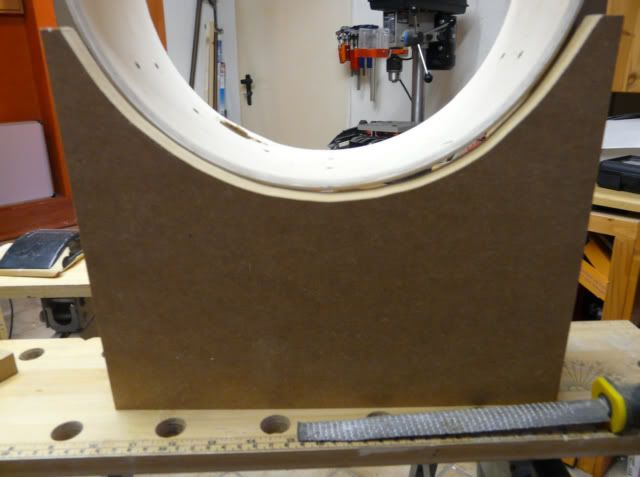
In meinem Fall befindet sich ein Böcken genau unterhalb und mittig des Toms. In folge Dessen, ist eine Nut, 40mm breit und 30mm tief, notwendig.
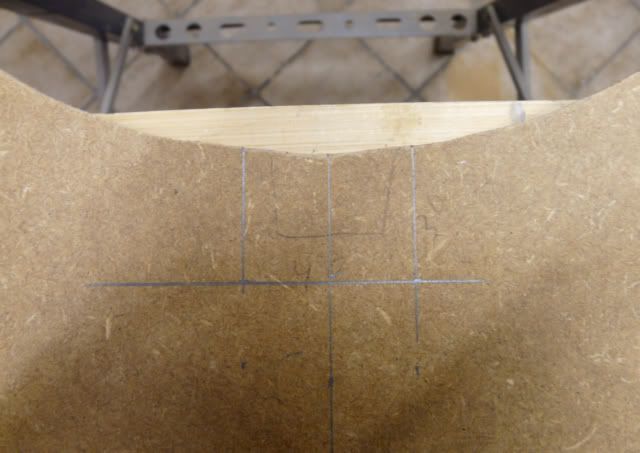
In den Ecken jeweils ein Loch bohren...

...und aussägen.
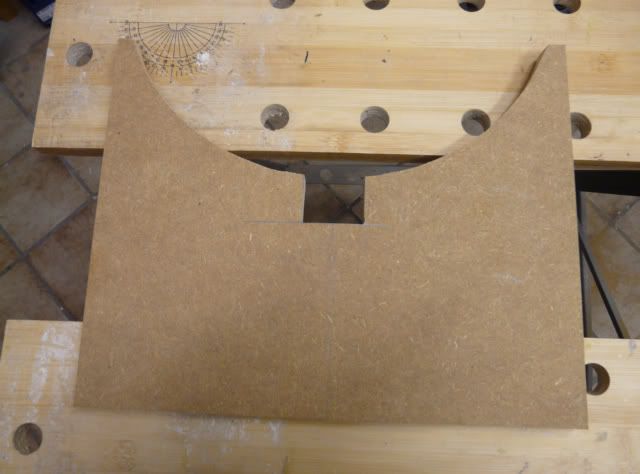
ACHTUNG: Fogende zusätzliche Maßnahmen sind unbedingt notwendig!
Ich habe zwar an die Aussparung für das untere Böckchen gedacht, jedoch nicht bedacht, dass die seitlich Böckchen ebenfalls einiges an Platz benötigen.
Daher unbedingt an diese Posion die Ecken absägen. Das Brett ist somit nur noch 210mm hoch
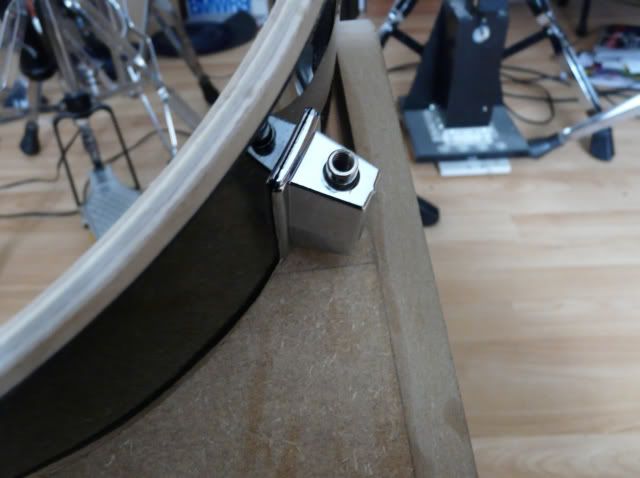
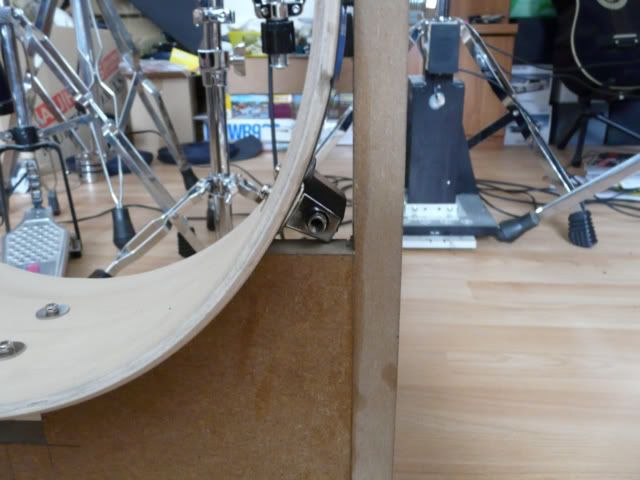
Nun ist es an der Zeit, die Rückwand an die Ständerbeine zu befestigen. Stumpfes kleben ist suboptimal, da doch einige Kräfte auf die Klebestelle einwirken. Drei Möglichkeiten stehen zur Auswahl
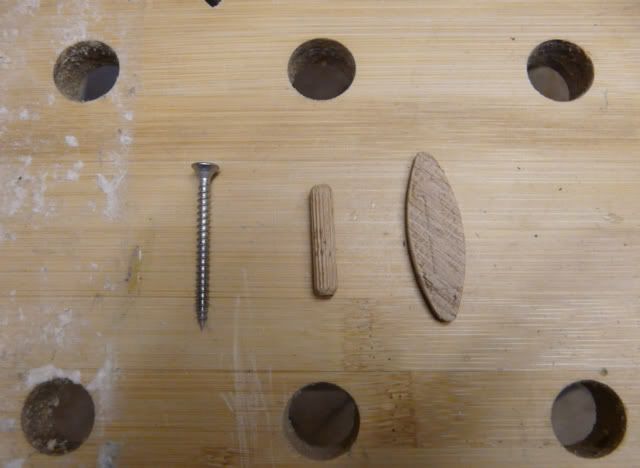
1.Verschrauben:
Bei einer Verschraubung, müssen UNBEDINGT vorgebohrt werden, da sonst das Holz ausreisst.
2.Holzdübel
Schwer zu verarbeiten, da Löcher sehr genau gebohrt werden müssen. Hierzu bietet der Handel eine speziell Schablone für ca. 15€
3.Lamellos
Die eleganteste Methode. Sehr stabil und wirkungsvoll. Der Nachteil: Man benötigt eine spezielle Maschine, die aber schon zum Preis von ca. 30€ erhältlich ist. Das Ding macht sich bezahlt, da man es im Laufe seine Lebens sicherlich mehrmals benötigt
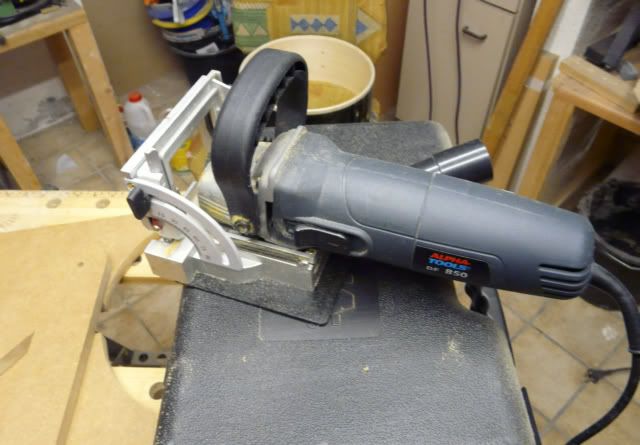
Die Nuten mit der (Flex) gesetzt
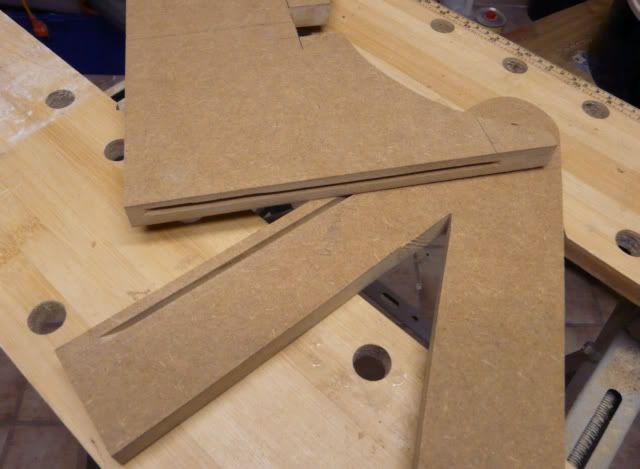
Erste Passprobe
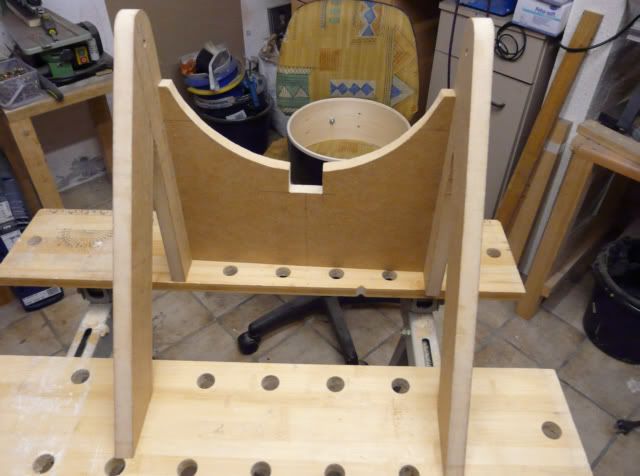
Der Rest ist Routine. Zunächst eine Flasche Ponal
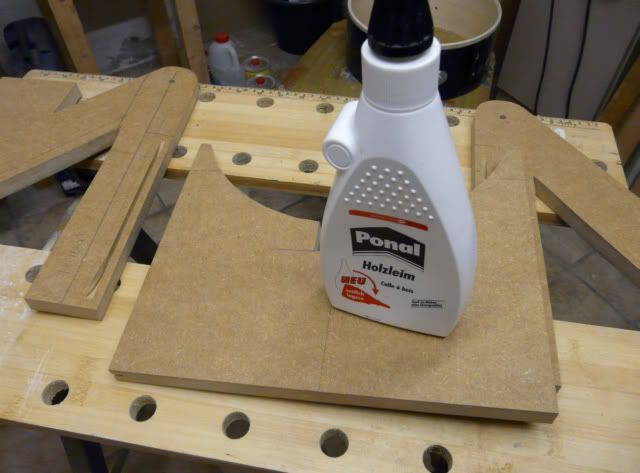
Die zu Klebenden Flächen sorgfältig einstreichen. Die Fingermethod ist dabei meiner Meinung nach immer noch am effektivsten.
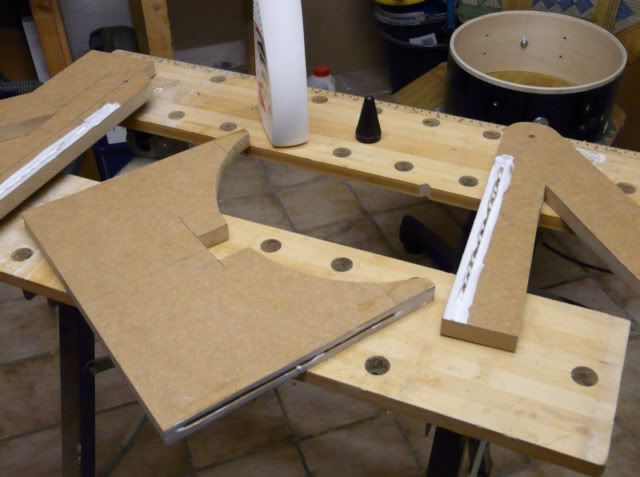
Nun Alles zusammenfügen und mit Schraubzwingen sichern. Jetzt wird auch der Nutzen des 310x90mm Bretts sichtlich. Es dient lediglich als Distanzhalter.
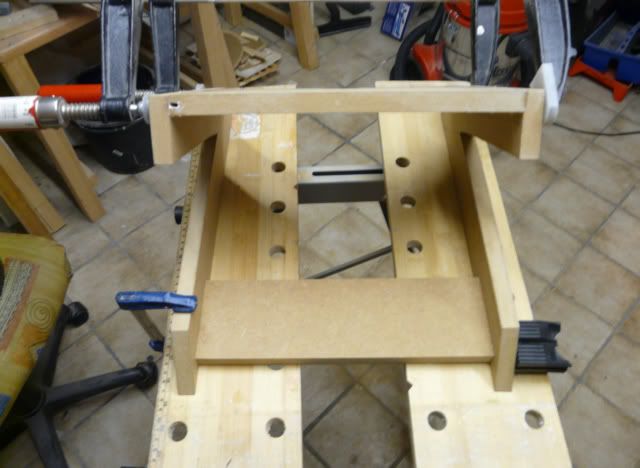
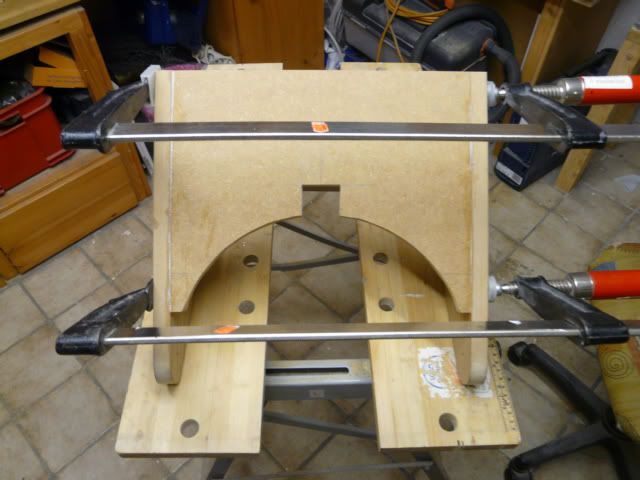
Zusätzliche Bilder:
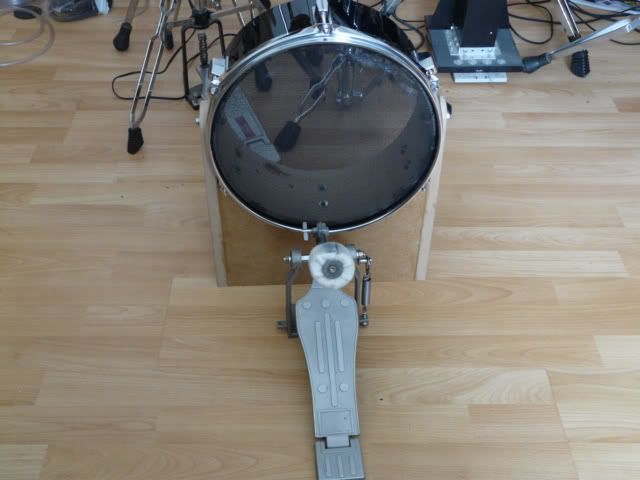
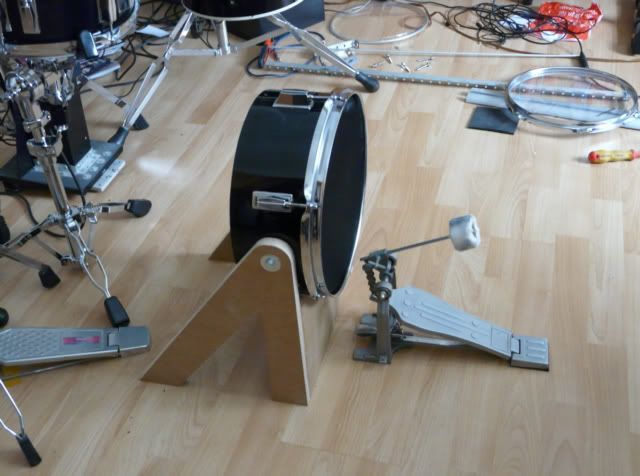
Im nächsten Schritt wird lackiert. Das erfordert Geduld. Wie das geht, erfahrt ihr nach der nächsten Maus.
7.2.2010 Teil 2: Fertig lackiert
Da ich ein großer Freund von Farbverläufen bin, habe ich mir ein Verlauf Schwarz/Silber ausgesucht. Von den Fluchereien, die man während eines Lackiervorgangs ausübt, will ich nicht bereichten. Am schwersten war wieder mal der Klarlack. Staubeinschüsse, schleifen, Staubeinschüsse, schleifen usw. Da möchte man schon mal lachend in die Kreissäge laufen. Hier die Bilder
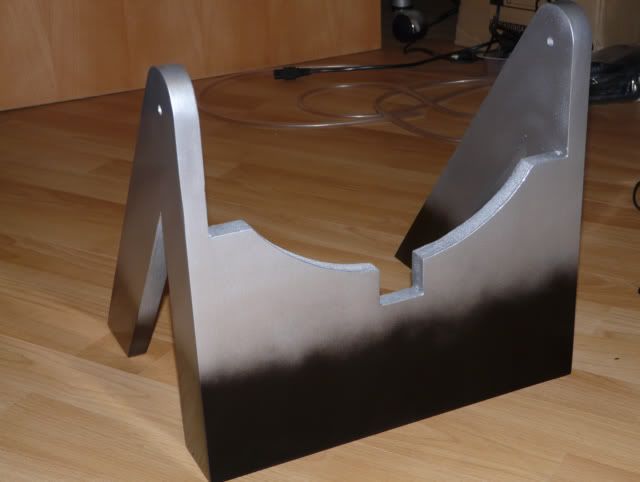
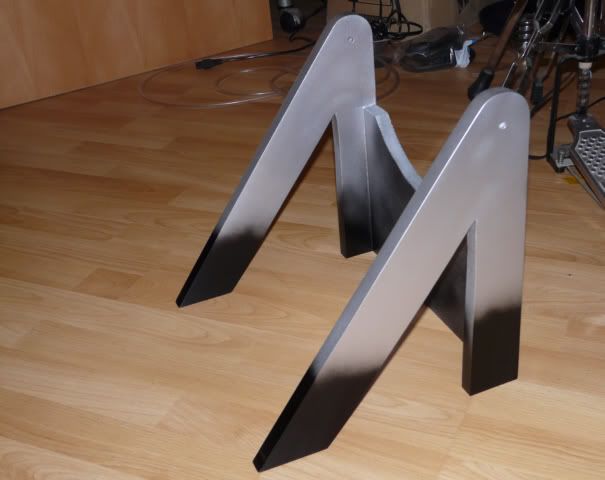
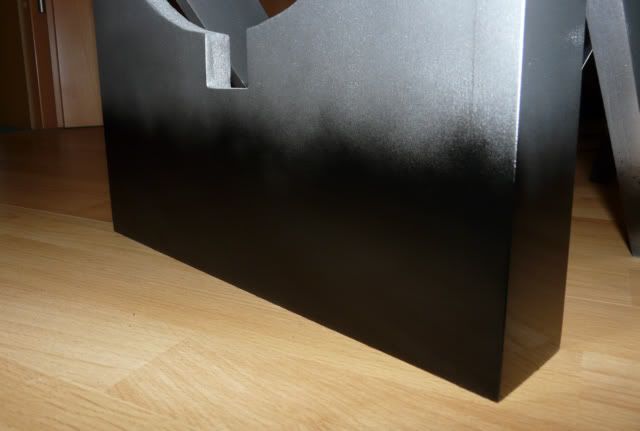
Und da es mir nie richtig gelingt Hochglanz in der Totalen ohne Blitz abzulichten, hier mal aus näherer Betrachtung:
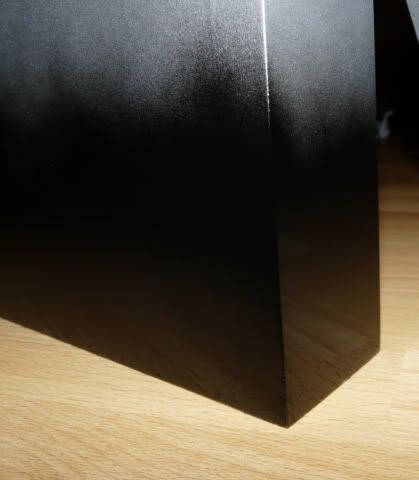
Ohne Blitz. ISO 800. Es rauscht und rauscht und rauscht.
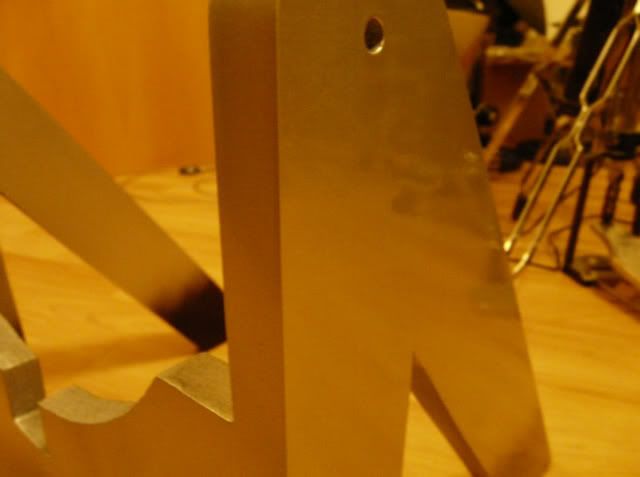
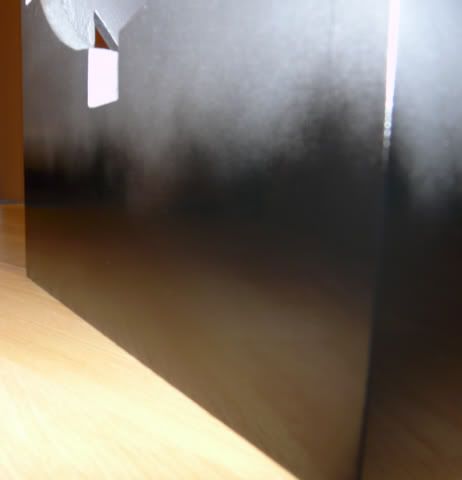
13.2.2010 Teil 3: Die Fußmaschinenkonsole
Benötigt wird ein Konstruktionswinkel 70x70x60mm, gab es kürzlich bei Lidl. Vier Stück zum Preis von zweieurodrulfzig. Weiterhinein Reststück Laminat 120x67x9,5mm, vier Schrauben M4x15 (oder 20), Muttern, Unterlegscheiben und Federringe.
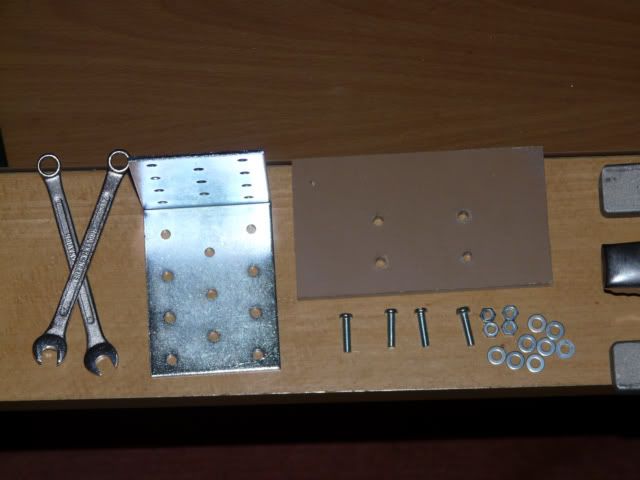
Die Löcher im Lamint werden direkt, durch auflegen auf den Winkel angezeichnet. Ich verzichte hier auf die Maße, da diese abhängig von der Lochmaßen des Winkels abhängen.
Nach dem Bohren, die Platte am Winkel schrauben und zur Probe anpassen und anschließend lackieren
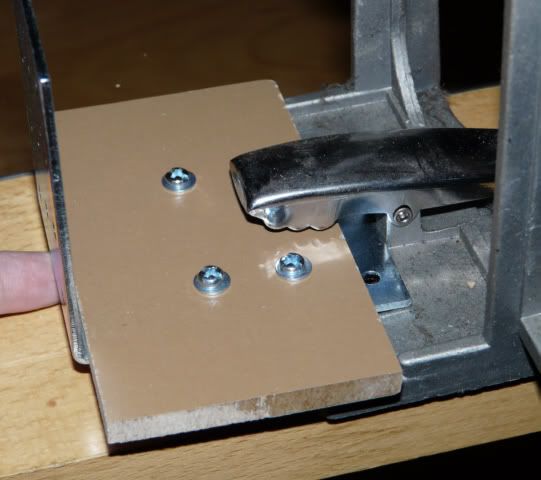
Für den nächsten Schritt, benötigt man fünf Holzschrauben 4x20mm, fünf Unterlegscheiben sowie ein 65 mm langes Stück einer Gummiwinkelleiste. Hier von Kantoflex, 5m zum Preis von 6,95. Der Rest wird später benötigt.
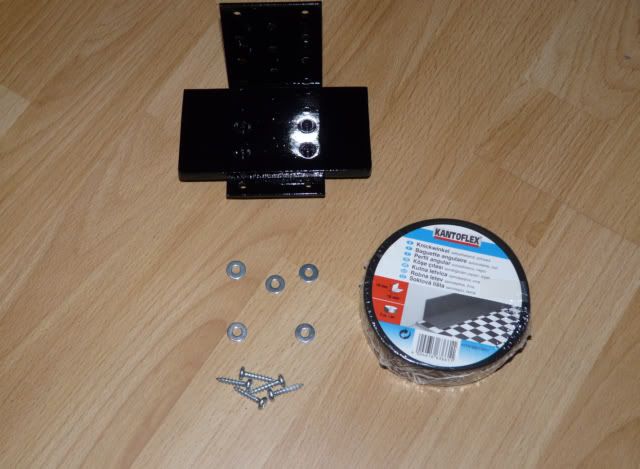
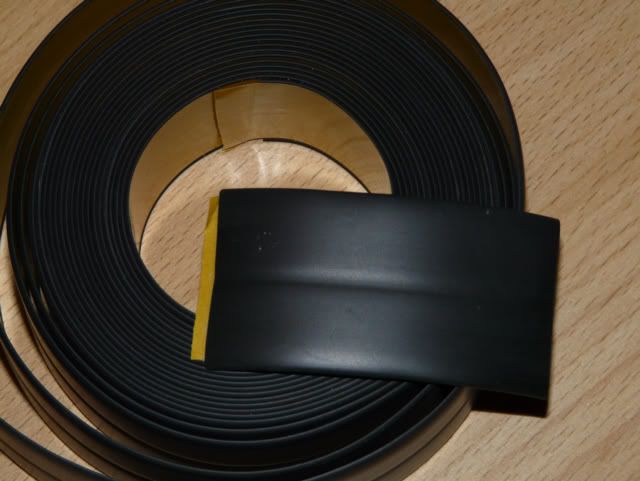
Dieses Stück Gummi wird mittig auf die Halteplatte geklebt.
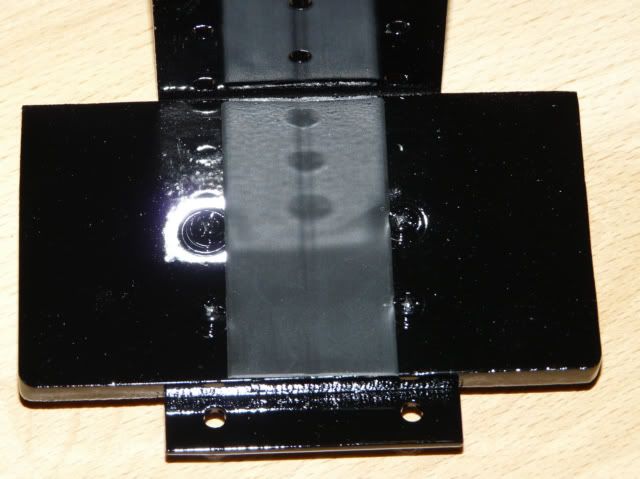
Nun zur Montage an den Ständer:
Die Fußmaschine wird an die Konsole befestigt, an den Ständer angehalten, genau mittig ausgerichtet und die Löcher mit einem, möglichst Farbintensiven Marker, gekennzeichnet und anschließend gebohrt. Immer wieder ein Ärgernis der Fotografie: Man sieht Staub, den das Menschliche Auge nicht wahrnimmt.
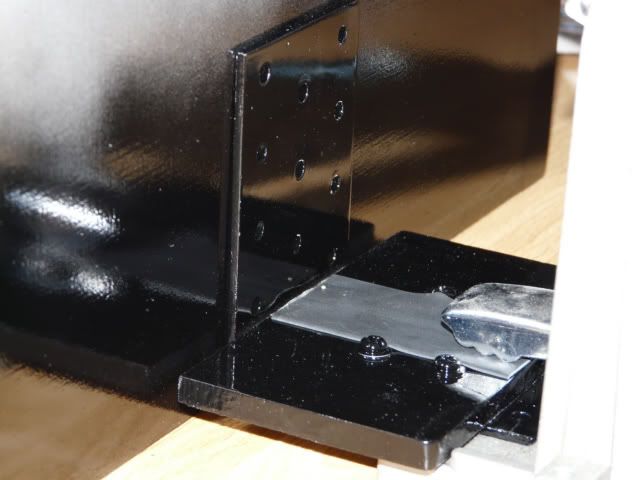
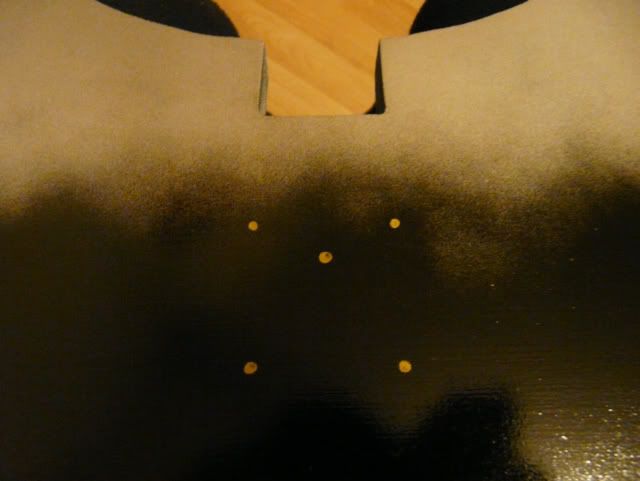
Mit den Schrauben und den Unterlegscheiben die Konstruktion an den Ständer befestigen.
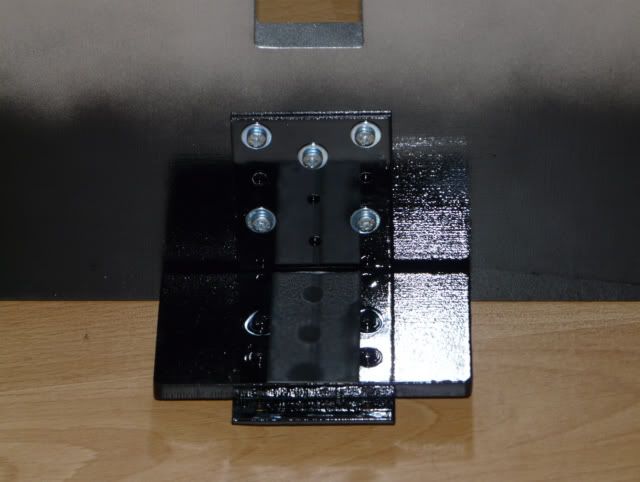
Et voilà
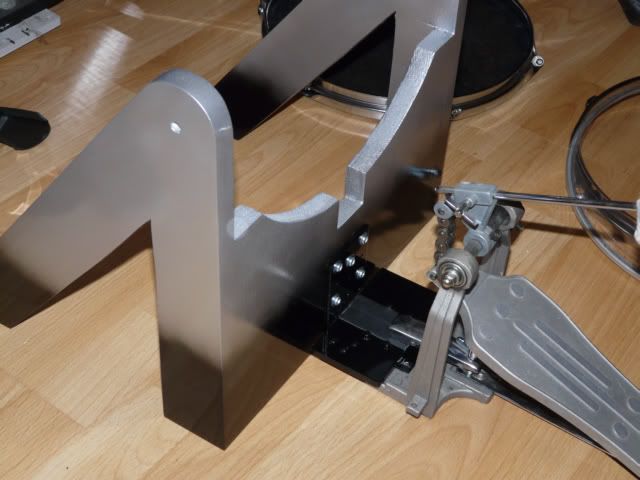
Da dieser Post doch nun sehr lang wird, geht es hier weiter. Also durchatmen, Kaffee trinken, Toilette und dann weiter:
Zu Teil 4: Die Triggerkonstruktion
Bis bald.
Gruß
Reinhold