Seid dem letzten Teil ist schon einige Zeit ins Land gegangen. Zum einen, lag dies daran, dass einige Arbeitsschritte sehr viel Zeit und Geduld benötigen zum anderen aber auch daran, dass Verbesserungen und Änderungen, die während der Entwicklung vorgenommen wurden, berücksichtigt werden mussten. So musste das Layout des Rückpanels komplett überarbeitet werden, da es in der ursprünglichen Form zu -ich nenne es mal infrastrukturellen Hindernisse- kam. Dennoch gibt es an der einen oder anderen Stelle Änderungen, die fotografisch nicht mehr zu Ändern waren. Ich weise dann explizit darauf hin.
Bei der Auswahl der Materialien, entschied ich mich für Birkenholz, da ich ein großer Liebhaber von modernen Technologien, eingepackt in edles Holz bin. Natürlich kann jedes andere Holz oder auch Metall verwendet werden. In diesem Fall sind die Maße entsprechend anzupassen.
Noch ein Hinweis zur Sicherheit: Da ich das Gerät auch USB unabhängig betreiben möchte, arbeitet es mit einer internen Stromversorgung. Ich werde diese Arbeitsschritte nicht kommentieren oder Fragen diesbezüglich beantworten. Auch lehne ich jede Verantwortung beim Nachbau ab. 230V gehören in die Hände eines Fachmanns sprich: gelernten Elektrikers.
Nun denn!
Für die folgenden Schritte, werden benötigt:
2x Multiplex Birke 320 x 250 x 9mm
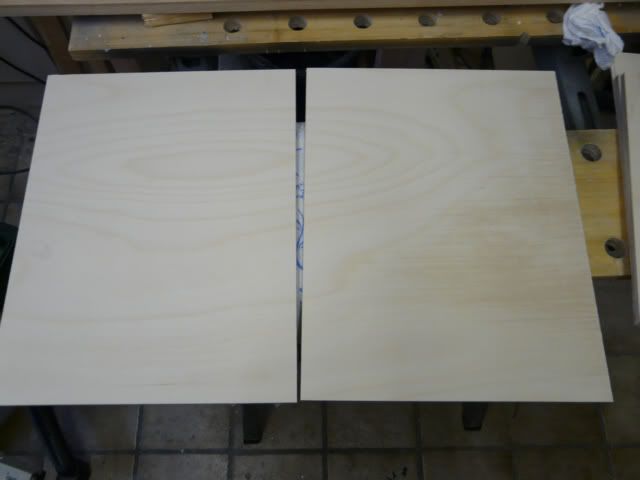
2x Multiples Birke 149,8 x 250 x 9mm
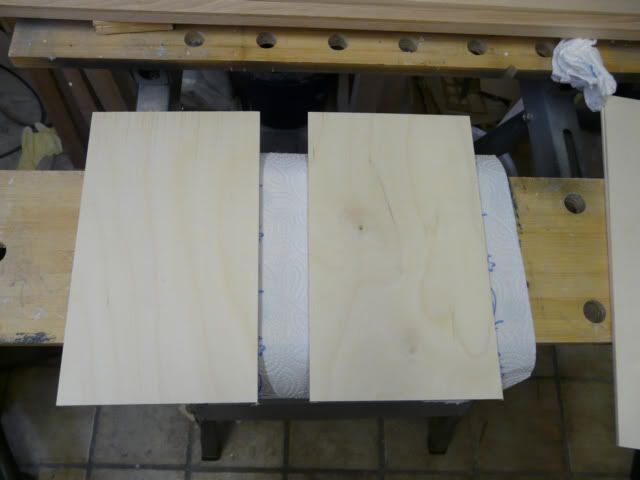

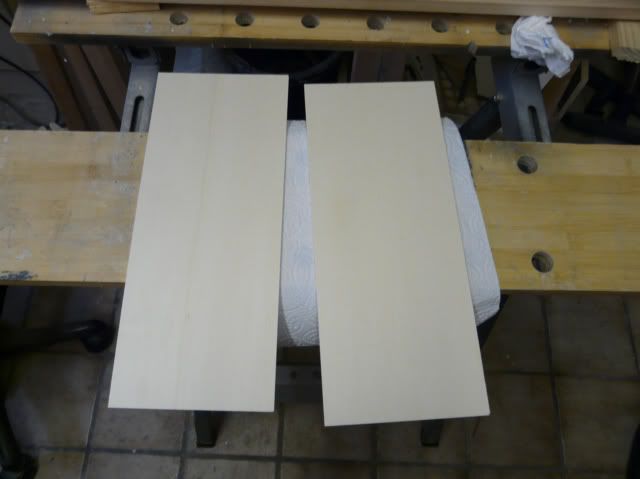
1 Meter Buchenkantholz 15x15mm
2 Meter Buchenrechteckholz 20 x 10 mm
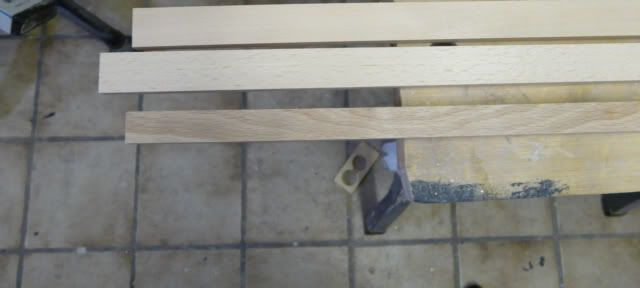
1 Packung Frontplattenfolie Conrad Nr: 530565
sowie 6 Holzschrauben Rundkopf 3,5 x 20 mm und 4 Senkkopfholzschrauben 3 x 20mm und etwas Tesa-Krepp
Entlang der 320er Breite, wird eine Linie bei 5mm am Boden, als auch am Deckel gezogen
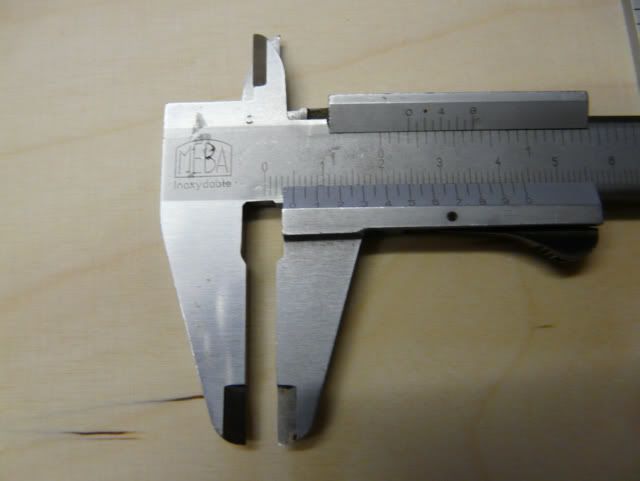
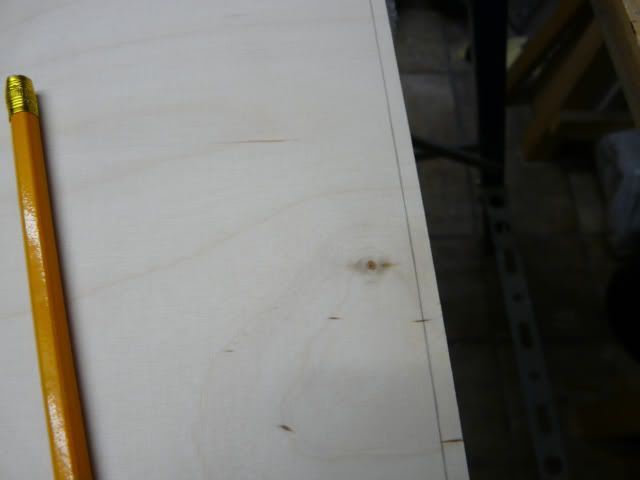
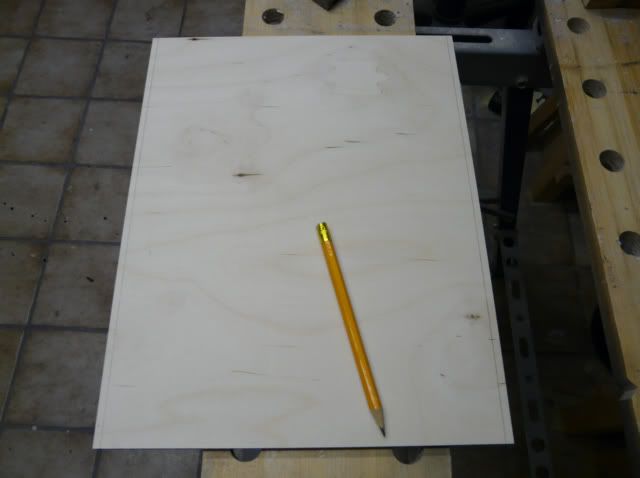
Das Maß dazwischen nehmen. Es sollte 240mm sein. Davon 2mm abziehen. Nun von dem 15er Vierkantholz, vier Stücke, mit je 238mm, sägen.
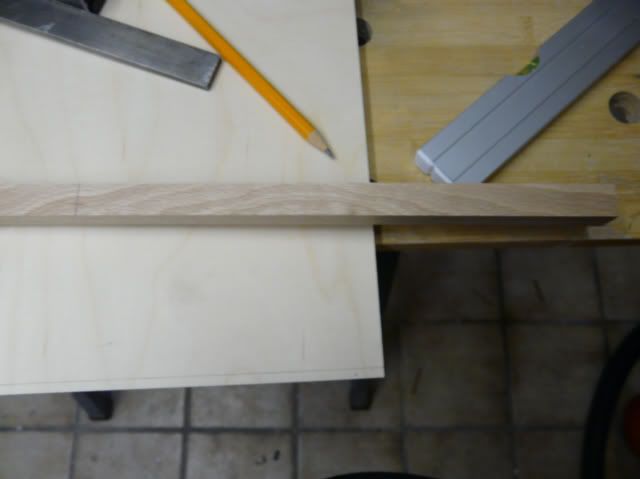
Boden und Deckel umdrehen und bei 7,5mm entlang der 250er Seite eine Linie ziehen
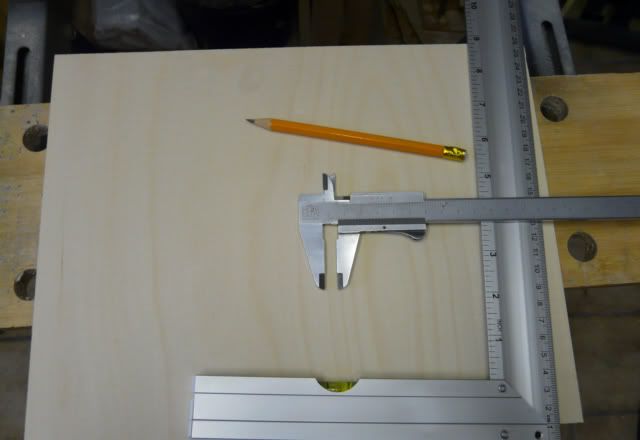
Beim Deckel, an den Positionen 25 und 225 mm eine Markierung an den beiden Linien anbringen. Beim Boden zusätzlich noch genau in der Mitte – also 125mm – eine weitere Markierung anzeichnen.
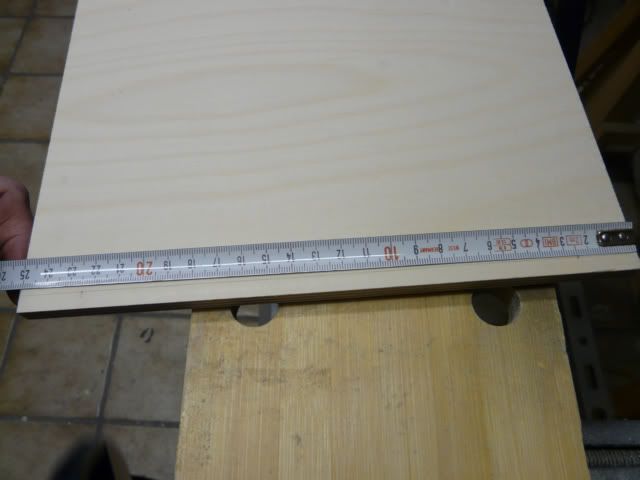
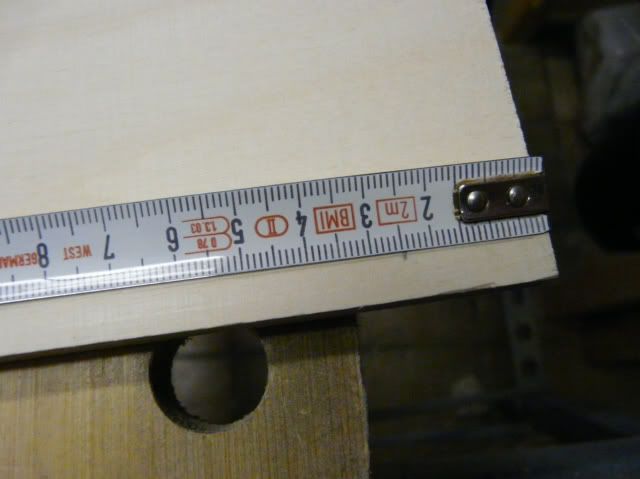
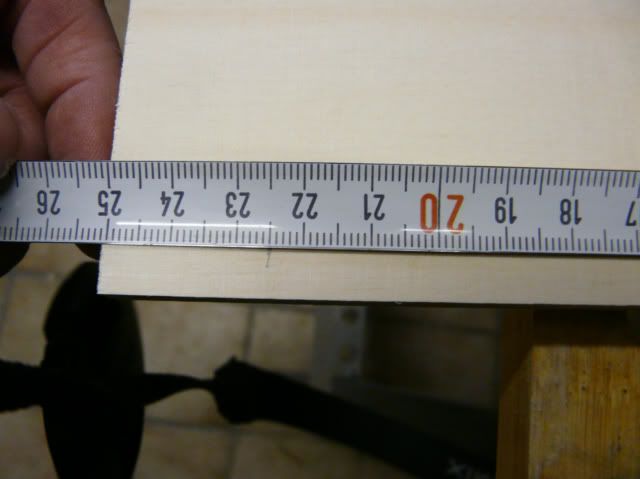
Nun an den Markierungen jeweils 4mm Löcher bohren und beim Deckel vorsichtig senken. Dabei immer wieder die 3mm Senkkopfschraube in das Loch führen um zu kontrollieren, wie weit gesenkt werden muss. Es sieht nicht sonderlich schön aus, wenn eine Senkkopfschraube im Holz verschwindet. Der Boden benötigt keine Senkungen, da er mit den Rundkopfschrauben befestigt wird.
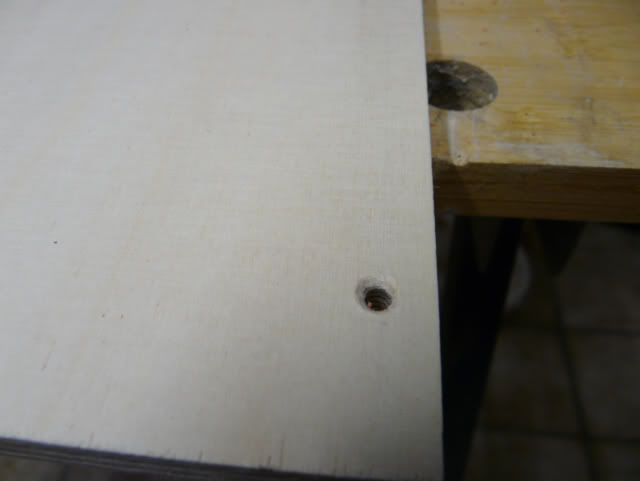
Nun die Vierkanthölzer, an den Rändern von Boden und Deckel, mit einer Schraubzwinge o.Ä. befestigen ...
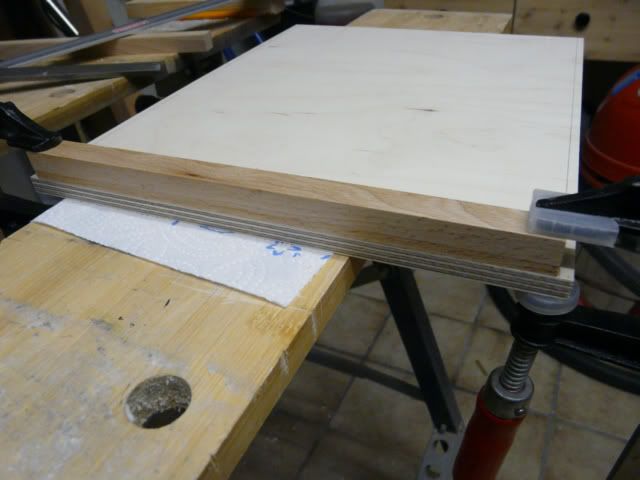
.. und mit einem 3mm Bohrer ...
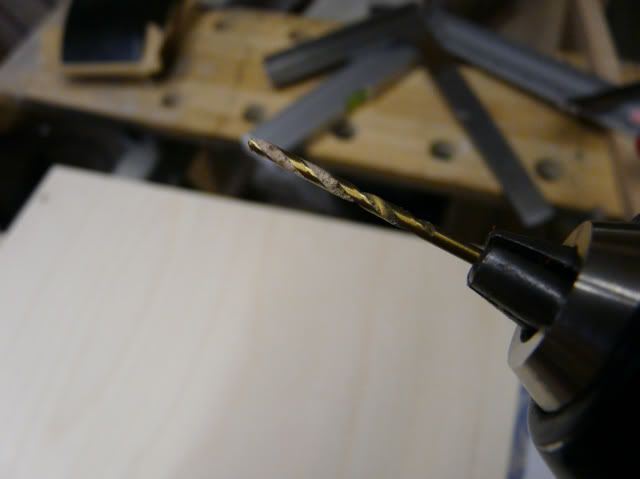
duch die vorhandenen Löcher bohren.
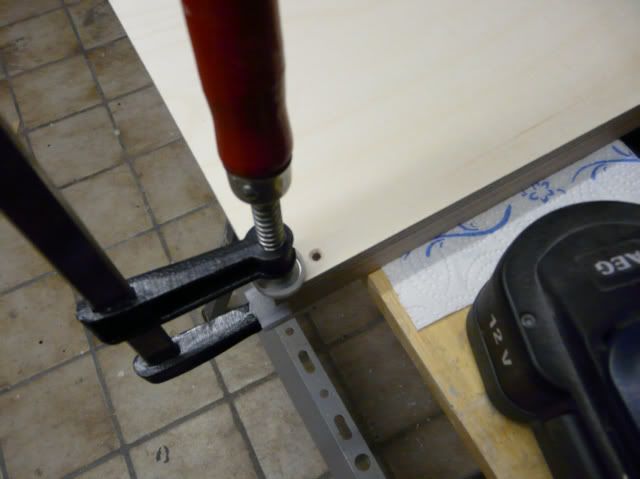
Anschließend, Deckel und Vierkanthölzer, mit den Senkkopfschrauben verbinden.
Im nächsten Schritt, werden von den Rechteckleisten vier 288mm lange Stücke abgelängt,...
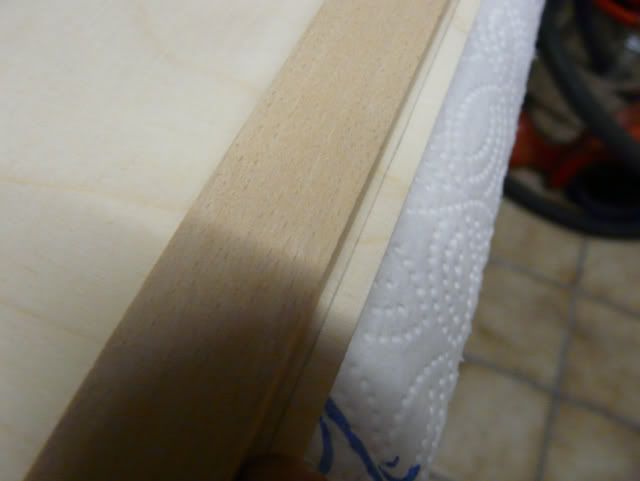
... sauber mit Holzkleber bestrichen ...
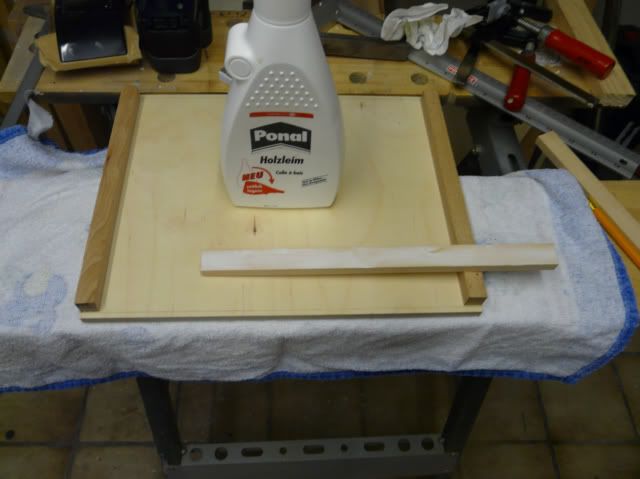
und mit Zwingen ordentlich am Deckel entlang der 5mm Linie gepresst.
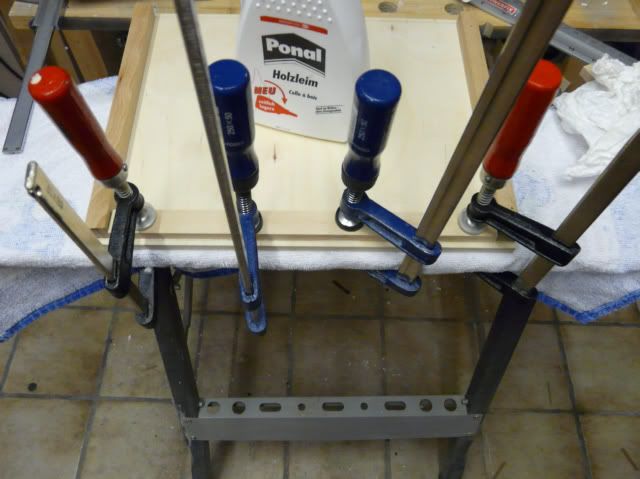
Die gleichen Arbeitsschritte werden mit dem Boden durchgeführen.
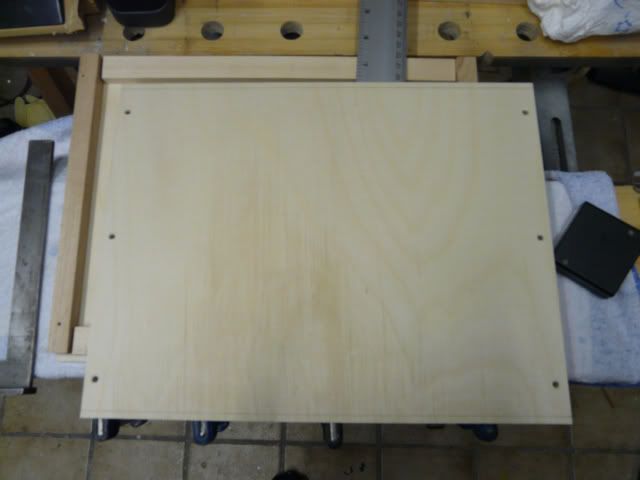
Hier der Boden als fertiges Teil.
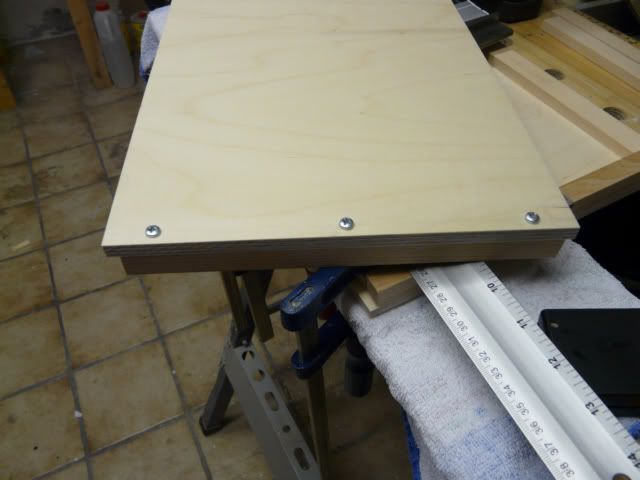
Sowohl Deckel als auch Boden werden an den Seiten mit Tesakrepp abgeklebt um zu verhindern, dass bei dem Verleimen der Teile, der Deckel oder der Boden mit verleimt wird.
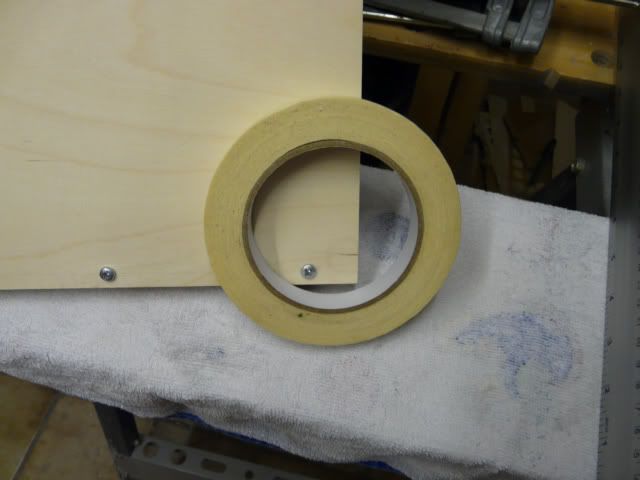
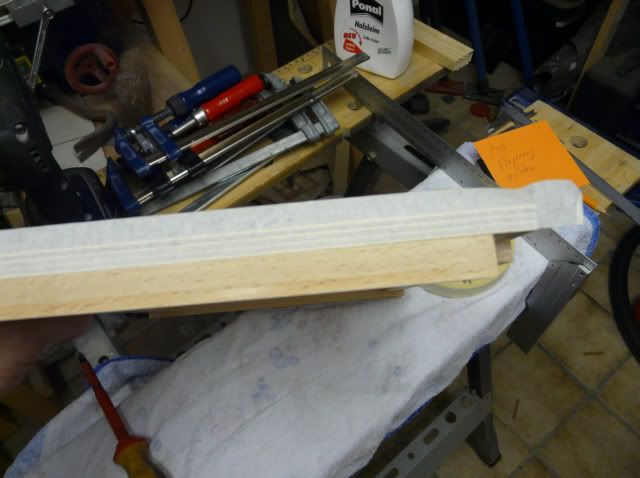
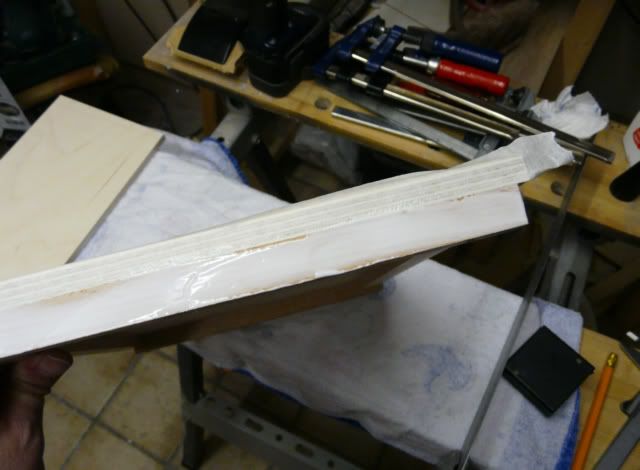
Nun können alle Teile miteinander verleimt werden.
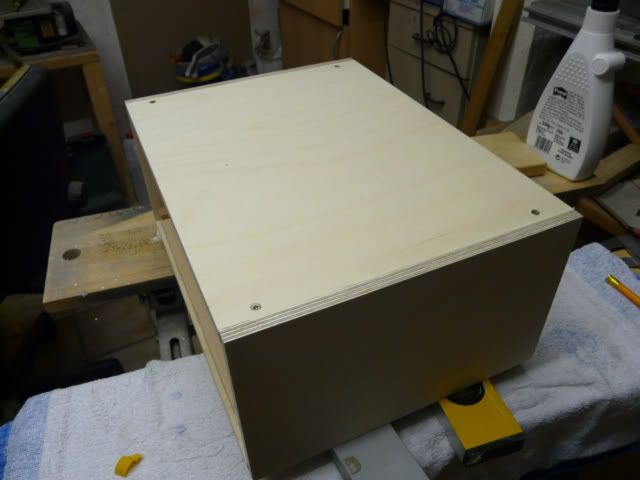
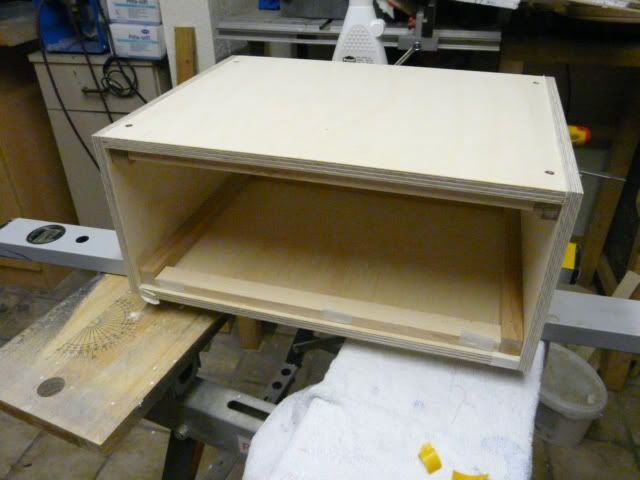
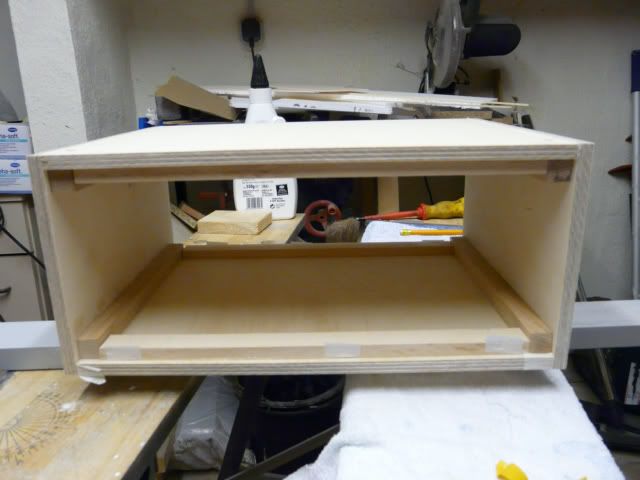
Nun folgt der zeitaufwendigste Schritt. Zunächst das Gehäuse komplett – ACHTUNG: In Faserrichtung- mit Schleifpapier 150er Körnung schleifen, bis sich das Holz glatt, sehr glatt anfühlt. Anschließend gründlich mit einem Tuch vom Holzstaub befreien und mit Holzöl satt einstreichen. Ja, es kann ruhig auf dem Holz schwimmen.
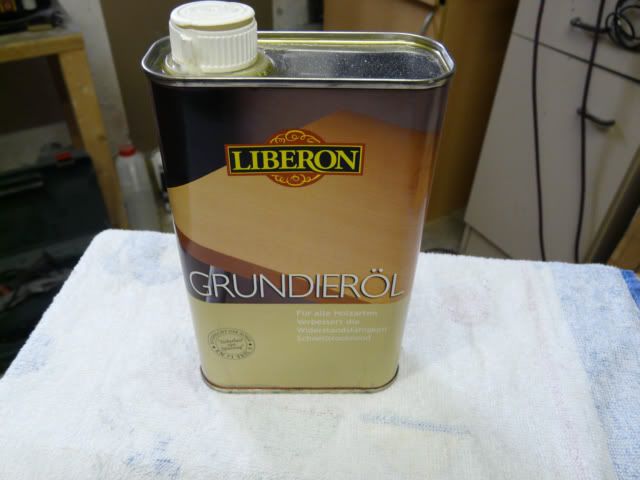
Nach ca. 30min., das restliche Öl mit einem fusselfreien Tuch abnehmen und ein Tag warten. Zu diesem Zeitpunkt ist das Ergebnis eher ernüchternd, da dass Öl tief in die Poren des Holzes fließt. Das heißt: Das Gehäuse ist matt oder anders, es sieht genau so aus wie vorher. Um einen seidenen Glanz und die Wärme beim Anfassen des Holzes herzustellen, wird nun mit 320er Papier gründlich geschliffen, bis das Holz wieder sehr glatt ist, dann wieder gesäubert, geölt und ein Tag gewartet. Im nächsten Schritt mit 600 Papier glatt schleifen, säubern, ölen, einen Tag warten. Nun mit 800er Papier schleifen, säubern, ölen, einen Tag warten. Im letzten Schritt nochmal mit 1000er Papier langsam und vorsichtig schleifen und säubern. Glaubt mir: Auf dieses Stück könnt ihr Stolz sein. Das erreicht man m.M.n. mit keinem Lack, mal abgesehen von den Nasen, die man als ungeübter Maler immer mal zieht. Mit Öl passiert so etwas nicht.
Nicht minder Zeitaufwendig, ist das Gestalten des Front- und Rückpanels. Bis man das so hat, dass es einem Gefällt, ist schon einiges an Geduld notwendig. Jedoch kann man den Zeitraum zwischen den Trocknungsphasen hierfür herrlich nutzen.
Zunächst wird eine Schablone, mit einem Grafikprogramm, erstellt. Hierbei sollten alle Teile, mit ihren Maßen, berücksichtigt werden, damit es keine bösen Überraschungen gibt. Nun die Schablone mit Sprühkleber auf das 3mm Pappelholz kleben und die zu Bohrenden Löcher mit einem Vorbohrer markieren.
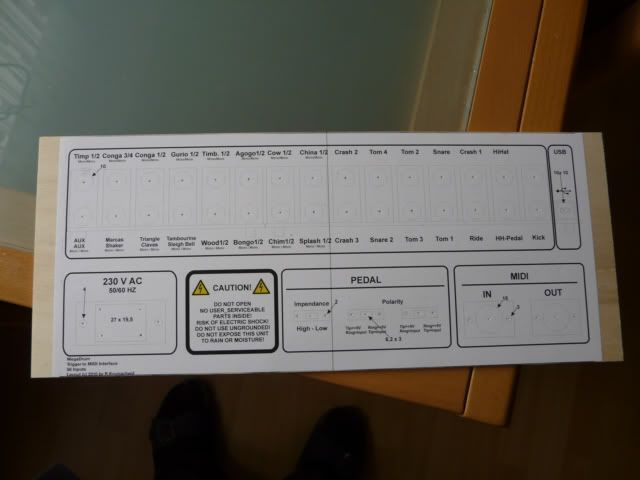
Soweit war ich ganz zufrieden, jedoch waren die Löcher für die Aufnahme der Klinkenbuchsen zu klein. Daher statt 10mm, 11 oder besser 12mm Löcher bohren
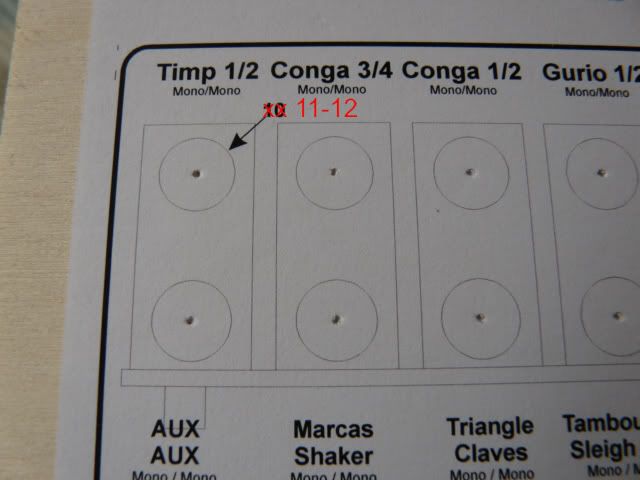
Am oberen Rand werden in gleichmäßigen Abständen 5mm von oben, 3mm Löcher gebohrt. Diese sind notwendig um die Panele an den Rechteckleisten des Deckels Deckel zu verschrauben um so eine höhere Steifigkeit zu gewährleisten.
An den Durchbrüchen, zusätzliche Markierungen an den Ecken anbringen, mit einem 4mm Bohrer bohren und anschließend mit einer Stichsäge o.Ä. aussägen.
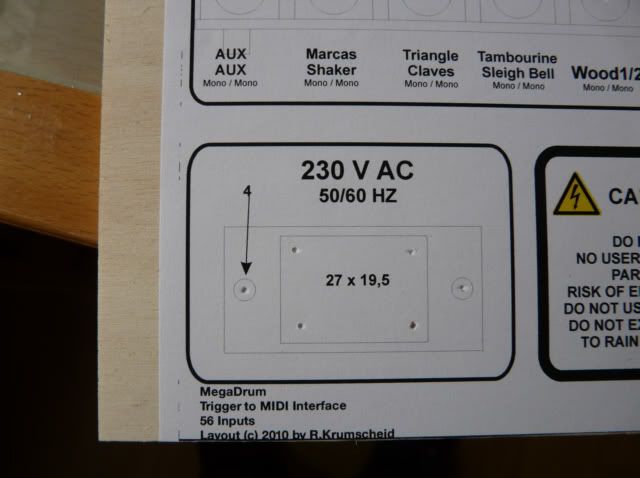
Nach dem Bohren und dem Sägen der Durchbrüche.
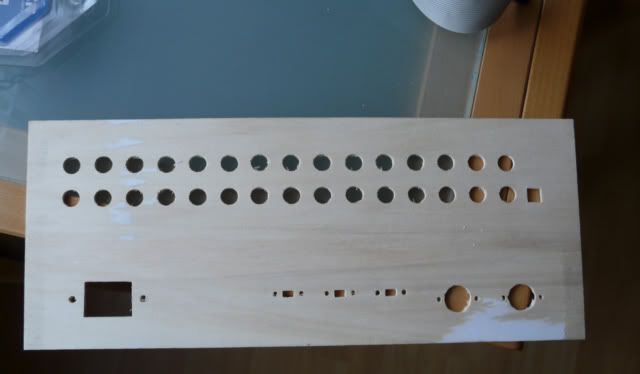
Sollten die Durchbrüche oder die Bohrungen nicht ganz sauber sein, so ist das kein Problem, da die Ränder bis zu einem gewissen Maß von den Gehäusen der Einbauteile verdeckt werden.
Eine erste Passprobe.
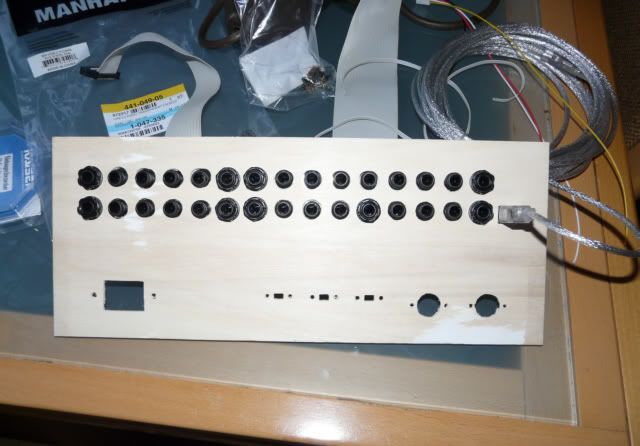
Nach der Passprobe, kann das Rückpanel mit der Farbe seiner Wahl, in diesem Fall Silber mit Klarlack überzug, versehen werden.
Eine Kopie der Schablone, ohne Maße und Bohrlochangaben, wird für die Endanfertigung auf die transparente Frontplattenfolie gedruckt. Vor dem Aufkleben auf das Panel, erst die Folie auflegen und gegen Licht halten um zu sehen, ob die Durchbrüche und Bohrungen sich decken. Dann Markierungen an Folie und Panel anbringen. Nun von oben nach unten die Trägerfolie abziehen die Folie, und sauber auf das Holz kleben.
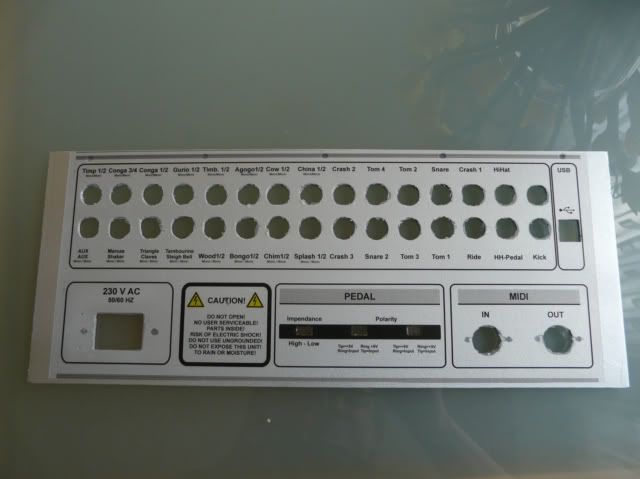
Mit der gleichen Technik, wird das Frontpanel gefertigt.
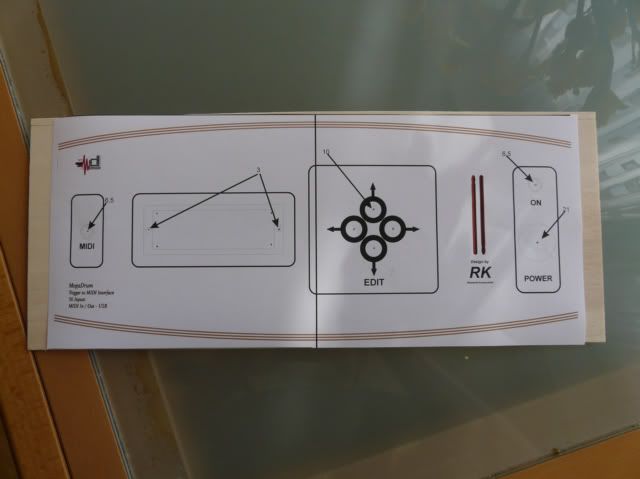
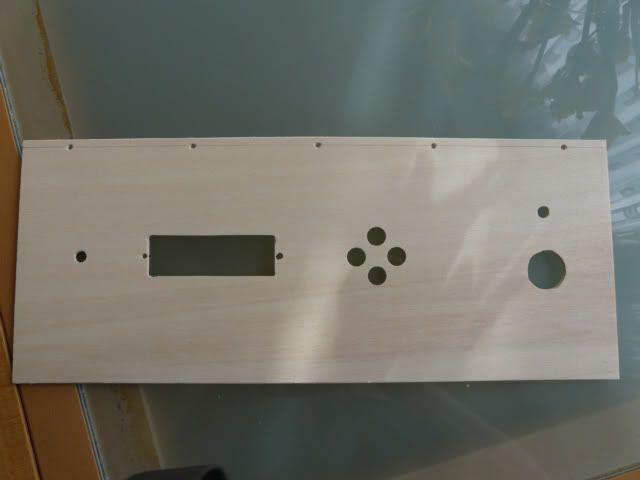
Nun kann das Rückpanel mit dem Gehäuse verleimt werden.
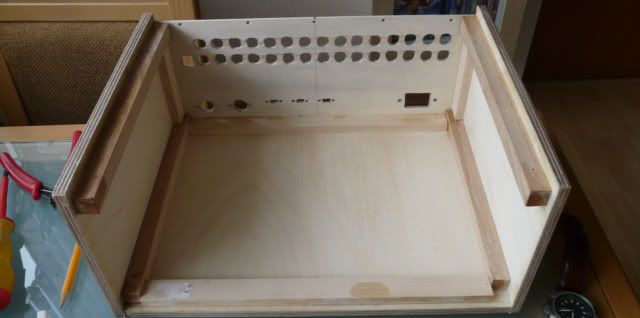
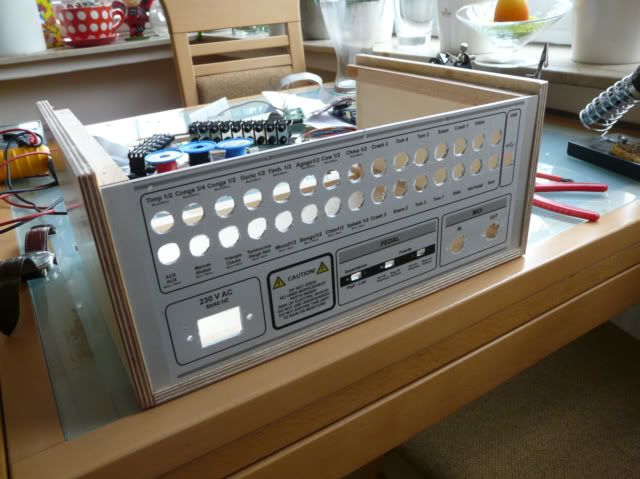
Soweit, so gut. Im nächsten Teil, wird das Gehäuse bestückt. Diesmal dauert es mit Sicherheit nicht so lang. Versprochen
Gruß
Reinhold
Hier geht es weiter zu Teil 4